Precursors to Empowering QARA Professionals with AI-Driven Technologies
Commentary Contributed by Denise Meade and Mike King, IQVIA
April 18, 2025 | As life sciences companies increasingly embrace artificial intelligence and digital transformation, quality assurance and regulatory affairs professionals face opportunities and challenges. The journey from paper-based systems to AI-driven solutions requires careful consideration of the various factors required to ensure successful implementation while maintaining global compliance and product quality to ensure the provision of safe and effective patient solutions and treatments.
The Digital Transformation Imperative
Gone are the days of endless paper trails, Post-It notes, and desktop paperweights. Digitization through electronic quality management systems is no longer just an option; it is a necessity. For life sciences organizations, eQMS streamlines processes and helps accelerate the innovation-to-commercialization pipeline. At the same time, eQMS supports a dual focus on ensuring patient safety while improving commercial performance. Companies without digital plans risk falling behind competitors as digital transformation enables better responses to evolving market conditions, advancing regulations, and critical customer needs while improving quality and patient outcomes.
However, the path to digitization has several key challenges. Many medical devices and in vitro diagnostic companies have grown through mergers and acquisitions, leading to multiple approaches for similar processes within the same organizations. This complexity necessitates thorough process evaluation during digital transformation. The key to successful transformation lies in identifying clear priorities that demonstrate measurable return on investment. During the initial transition from paper-based systems to eQMS, it is crucial to identify and invest in the most significant priorities first. Demonstrating return on investment secures both senior stakeholder buy-in and broad-based employee acceptance during digitization programs, which are often accompanied by significant changes in organizational culture.
Empowering Quality Assurance and Regulatory Affairs (QARA) professionals to take advantage of this new, fast-paced technological environment requires putting strategic elements in place to drive real-time operational benefits.
Process Harmonization: The Foundation for Success
Before deploying electronic systems, a critical first step is to harmonize processes and evaluate data structure. No digital system acts in isolation from existing infrastructure. Deploying a digital solution without taking into consideration company processes will either result in significant mismatches between existing practices and electronic workflows or set in concrete existing inefficient ways of working that may inhibit company performance and organizational growth.
Within the organization, the eQMS should not be viewed as the deliverable but rather as a facilitator of business objectives, whether enabling faster operations or ensuring safe, cost-effective product delivery. If digital solutions become more expensive or inefficient than analog methods, organizations may face resistance to their adoption.
Organizations can learn from previous enterprise resource planning deployments and avoid simply recreating existing problems in new systems. Strong governance and control mechanisms ensure that deviations from agreed deployments are necessary and scalable across the organization and are not bespoke fixes for local issues.
Modern system deployments should be designed with flexible architectures to accommodate both legacy systems and future technological advances. Organizations upgrading or consolidating systems after mergers and acquisitions benefit from adopting a modular approach. QMS, ERP, and product life cycle management systems must function as part of an integrated ecosystem with seamless information flow. This integration requires systematic, iterative upgrading with a conscious understanding of the impacts of broad change management activities, allowing business operations to continue during transition to the new steady state of digital infrastructure. Furthermore, this approach allows organizations to improve incrementally while demonstrating success in process improvements, which generates project goodwill.
Identifying Separate Versus Harmonized Processes Following Mergers & Acquisitions
Industry mergers follow two main paths: control-based and selective harmonization. Control-based integration occurs when acquiring companies find quality issues during due diligence or seek operational efficiency through standardization.
Selective harmonization is common in larger medical device acquisitions where diverse products, geographies, and regulations prevent one-size-fits-all solutions, which leads to targeted standardization at division or process levels.
Understanding organizational history provides context for process decisions and prevents recreating past problems. Each harmonization choice has costs requiring evaluation. Effective change management is essential, though not everyone will adapt.
In healthcare, regulatory compliance cannot be bypassed. Context is crucial for medical device harmonization decisions, as the industry’s 500,000+ product types have varying risk profiles and regulatory requirements that influence standardization choices. Ensuring the right company stakeholders, inclusive of global QARA professionals, are involved in a company’s M&A activity is key to optimizing QMS harmonization, where and when it occurs.
Balancing Process Variation Versus Standardization
The relationship between process variation and standardization mirrors broader technological decisions about automation versus human intervention. Process variations manifest differently across the product life cycle, from early research through clinical development, regulatory approval, manufacturing, and deployment to healthcare providers. Each stage presents unique challenges further complicated by geographic and therapeutic differences.
Starting with variation, organizations can use digitization to gather data that identifies standardization opportunities. Understanding variation origins is essential before determining standardization potential, allowing systematic reduction while preserving necessary differences for product quality and patient safety.
Industry approaches have evolved through distinct phases: digitization gained momentum 15-20 years ago, automation became prominent in recent years and AI continues to advance. These elements work together synergistically to achieve effective process standardization. Successful standardization requires diverse stakeholders who have historical and forward-looking perspectives. Technology and subject-matter experts can balance competing needs with digital solutions focusing on both patient safety and commercial performance.
Organizations face challenges from risk-averse stakeholders who may misrepresent requirements as specifications. Clear vision-setting and idea pressure-testing help navigate between uncritical agreement and irrational rejection, while focusing on customer problems and maintaining appropriate process variations.
Beyond Data Lakes and Toward Domain-Driven Integration
Modern data management requires a shift from centralized systems to more flexible, domain-specific approaches. Organizations are discovering that trying to consolidate all data into a single system or data lake isn't always the best solution because it can sacrifice necessary data or create an extraneous data collection burden. Instead, a data mesh strategy, which organizes information by product domains or functions while enabling robust cross-system integration, often proves more effective.
This approach recognizes the varying complexity of data across different products and systems and accelerates data delivery through a more decentralized approach. For instance, managing data for a simple medical device like a scalpel requires tracking just a few variables, while complex equipment like X-ray machines demand sophisticated data architectures to handle multiple configurations, mounting options and software versions. These differences illustrate why a one-size-fits-all approach to data management often falls short.
Interface connectivity emerges as a critical factor in successful data management. Organizations need their systems to communicate not only internally but also with regulatory agencies and industry partners. Poor integration can lead to costly inefficiencies, such as the redundant entry of identical information across multiple ERP systems. Cloud-based solutions can help address these challenges, but it’s crucial to implement proper integration strategies from the start, because fixing issues later can be significantly more expensive and potentially detrimental to regulatory compliance.
The approach to data management should mirror manufacturing’s continuous improvement principles, with ongoing incremental enhancements rather than dramatic overhauls. This allows organizations to maintain business continuity while steadily improving their systems. When presenting data insights to stakeholders, the focus should be on commercial metrics like revenue growth or operational improvements, such as reduced product defects, while avoiding alarmist messaging that might hinder productive discussion.
Prioritizing Investments and Maintaining Focus While Managing Scope
The goal is to create a balanced system that maintains data integrity while remaining flexible enough to adapt to changing business needs and technological advances. This requires analysis of how data is organized, integrated and utilized across different domains and systems.
QARA professionals should prioritize and communicate value in commercial terms—growth, profitability and efficiency—rather than just compliance. Quantifiable metrics like reduced regulatory fines, improved quality, throughput, and faster response times build compelling business cases. Effective strategy involves deciding what not to do, with investments justified through business value assessments and ROI analysis that leverages inputs such as cost of quality and cost of non-quality.
Key value drivers include enhanced product quality, faster development cycles, reduced non-quality costs, and minimized regulatory risks. Organizations must quantify these benefits in dollars to prioritize effectively. The adoption of digital transformation should balance investment size, implementation challenges, and timelines to demonstrate value at various stages.
Scope management is critical as projects evolve and personnel change, with reference markers needed to prevent additions that dilute core deliverables. Organizations must balance cost, quality, and time—focusing exclusively on either small wins or larger strategic objectives can be problematic.
Organizations can adapt existing industry solutions, like complaint handling systems, rather than starting from scratch, and focus resources on differentiation that provides competitive advantage.
Looking Ahead: The Role of AI
Often, process digitization and basic automation should precede AI implementation, with investments evaluated based on size, difficulty, and timeline. Organizations exploring AI for complaints, document management, and regulatory submissions should focus on solving fundamental challenges rather than seeking technological silver bullets. Successful AI implementation requires well-structured processes and clean data, a clear understanding of where automation adds value vs. human expertise and a balanced approach between quick wins and strategic objectives.
The journey demands patience, resilience, and experienced leadership that understands diverse products, processes, and global regulations. Success is achieved by maintaining core deliverables while skillfully managing scope and expectations to focus on patient safety, operational efficiency, and commercial performance.
Denise Meade’s leadership builds upon over twenty years of experience in healthcare, life sciences, and technology, encompassing finance, strategy, product, and sales. Denise held management positions at Microsoft, IBM Watson Health, and Parexel, where she led the development and launch of novel solutions in digital health, clinical development, and real-world evidence. Denise holds a BS from Northeastern University and an MBA from Harvard Business School.
Mike King is Senior Director, Product and Strategy (Quality, Regulatory, Safety & Detect) Digital Products and Solutions at IQVIA With over 20 years of experience leading global teams in quality assurance and regulatory affairs, Mike King, as Senior Director of Product and Strategy at IQVIA, ensures healthcare solutions meet complex global regulations and oversees platforms like SmartSolve eQMS and RIM Smart to streamline quality and regulatory compliance processes. His email address is michael.king@iqvia.com.
Leave a comment
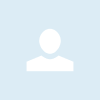
